
If you grocery shop in the Northeastern US, there’s a high chance you’ve come across Little Leaf Farms‘ salad greens in the produce section. The 10-year-old company, which has built a “hands-free growing” system inside its greenhouses, now commands more than 50% of marketshare among indoor lettuce growers. Little Leaf greens grace the shelves of around 8,000 grocery stores in New England and the mid-Atlantic states.
The company’s success is a welcome story, given indoor agriculture’s recent past dotted with bankruptcies, closures, and troughs of disillusionment largely related to vertical farming startups.
Greenhouse operations haven’t been totally immune to the market correction, but Little Leaf Farms CEO and founder Paul Sellew has a simple explanation for why they haven’t flailed quite as badly.
“The sun is an amazing resource with all of these benefits. Any logical approach to growing a plant would include the sun.”
Still, Sellew is not one to gloat over corpses of other companies, preferring instead to keep his focus on his own operation, growing plants and providing a consistent experience for customers.
Last month, the company broke ground on it’s third greenhouse, which will operate out of Manchester, Tennessee and serve the Southeastern states, beginning in 2026.
AgFunderNews caught up with Sellew this week to discuss the company’s expansion, the role of tech in indoor agriculture, and why there may actually be a sustainability argument for plastic packaging.
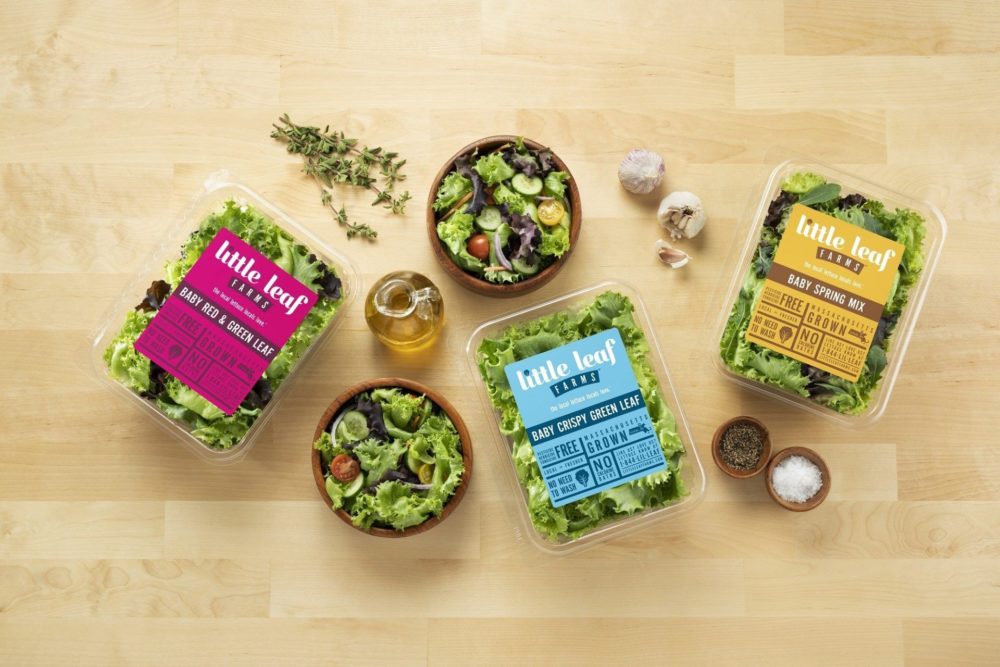
AgFunderNews (AFN): How has Little Leaf Farms weathered the ongoing tough times and kept making reliable products?
Paul Sellew (PS): There’s this boring thing called day-to-day execution, and it’s quite essential if you’re going to build a successful CEA [controlled environment agriculture] company.
We operate seven days a week, 365 days a year, and we’ve organized the humans around the plants, not the other way around.
AFN: What do you mean by that last point?
PS: Plants grow every day. As a result, running a system—seeding, harvesting, etc.—has to be consistent with the rhythm of how the plants are responding, and we organize humans around that concept.
As a result, the greenhouse is more or less the same, whether it’s the middle of winter or the middle of summer. We just created this controlled environment where the plants are happily growing.
We’re also at a scale where a cold chain is followed, and we’ve got great people that know what they’re doing, which then leads to a consistent eating experience for the customer.
[This approach of “boring day-to-day execution] is not unique to Little Leaf, although it’s amazing that it seems like a hard lesson to get for a lot of companies.
AFN: Do you think there’s an advantage of greenhouse growing over vertical farming?
PS: We’ve always believed that high-tech greenhouses were the were the solution and vertical farming was in search of a problem that didn’t exist.
The greenhouse industry was here beforehand. It’s here now, and it’ll be here in the future. There’s a very simple reason for this: the sun is a amazing resource with all of these benefits. Any logical approach to growing a plant would include this free resource.
The notion that vertical farming is higher technology [than greenhouses] is simply not true. The greenhouse industry is very sophisticated from a technology standpoint. Our facilities are fully automated, but when it comes down to growing plants, it never made sense to me that you would design a system around not using this free, amazing resource called the sun.
What’s been born out of this, unfortunately, is that many of these companies—not exclusively but predominately vertical farms—have gone bankrupt and failed.
There are other companies though. AppHarvest did not succeed as a company, but all those greenhouses [previously built by AppHarvest in Kentucky] are in operation today. You don’t see vertical farms that were shut down back in operation.
I think a lot of what we’ve seen here is this sort of arrogance around technology—what I’ll call the Silicon Valley mindset that says “agriculture is broken and we’re going to come in with our disrupter mindset.”
That didn’t work. A lot of these companies literally labeled themselves as tech companies when their business model was to sell leafy greens. To me, that was business model confusion.
AFN: How deeply is tech embedded into Little Leaf’s day-to-day operations?
PS: We are a tech-enabled company. We’re very conversant in technology—I think we’re recognized as probably the technology leader [in greenhouses]—but we are not a tech company.
We have full automation from from seeding to harvest; I would call that table stakes now. We’re beginning the process of automating our packaging, and then from there, there’s these emerging tools. We live in this AI-obsessed world now. We’re evaluating these next level tools to see what they can do.
But we are still a believer right now that great people are the differentiating factor, and we are highly dependent upon our very skilled and dedicated people.

AFN: Why did you choose Tennessee as the location for the new farm?
PS: There are areas of highly concentrated production, like the Salinas Valley [in California]. But should that one valley feed the entire North American continent its leafy greens?
If you live in the eastern half of the United States, you are dependent upon this little valley for lettuce.
Similar to what we’ve done in New England and the mid-Atlantic, and what we’ll do in the south, we now have the ability to service half the United States within 24 hours.
And so the basic value proposition [for the Tennessee farm] was the same as day one: provide a higher-quality, fresher eating experience, which we think is the food system transformation that’s going on right now.
We think a transformation would be returning these perimeters of urban markets—that used to be called farms and are now called suburbs—back to their historical role, which was to feed the neighboring cities. Put in high-tech greenhouses that produce 30 to 40 times the amount of food per acre (as traditional farming).
AFN: What’s the story with all the plastic packaging from greenhouse-grown lettuce?
PS: We’ve considered alternate packaging, but we’re also very focused on our customers. Some of them are completely driven by packaging, but right now I think that’s a a small minority.
Customers want to look at the product. So we could have an opaque tub, but that would deny people that experience of looking at the product to make sure it’s fresh.
We have elected is to stay with PET #1 [Polyethylene Terephthalate], which is the most widely recycled plastic polymer in the world.
I recently hired a student who tracked Little Leaf’s plastic tubs, from going to the recycling bin to a material recovery facility, to making a bale and going to a reclaimer that would grind that up, remove the label and the glue, spin-dry it, and have it go back to my thermoformer in Leominster [Massachusetts], and turn that into a tub again.
There is a misperception around the environmental benefits of plastic. I know it’s the material that people love to hate, but it offers some really unique experiences to the consumers. And if you manage plastic in the way that we are managing it, I think there is a strong argument for sustainability,
AFN: What excites you the most these days about indoor growing?
PS: I was formerly in the tomato greenhouse business, and over the last 40 years, certain tomatoes have really done a hard shift from field production to CEA production. I believe this will happen with leafy greens as well, and I think we are still in the in the early stages of that.
CEA-grown leafy greens are about 7% of the total market, and in North America, Little Leaf Farms represents over half of that. Literally, we grow more than all the other CEA leafy green companies combined, and we just think that we’re going to continue to grow in a measured way. We’re in 8,000 grocery stores now, servicing 53% of the US population.
AFN: Would you ever consider growing other crops?
PS: There’s still a big untapped market opportunity around leafy greens and the adjacent products, such as kits and all of that. So we see no reason to divert our focus.
AFN: So no growing watermelons or wheat indoors?
PS: We’ll leave that to others to blaze those trails, and wish them great success. In the meantime, we’ll be focused on leafy greens.
The post Little Leaf Farms’ CEO on building an indoor ag business: ‘Any logical approach to growing a plant would include the sun’ appeared first on AgFunderNews.